Micon Seals
HT SERIES SEALS SPECIFICATIONS
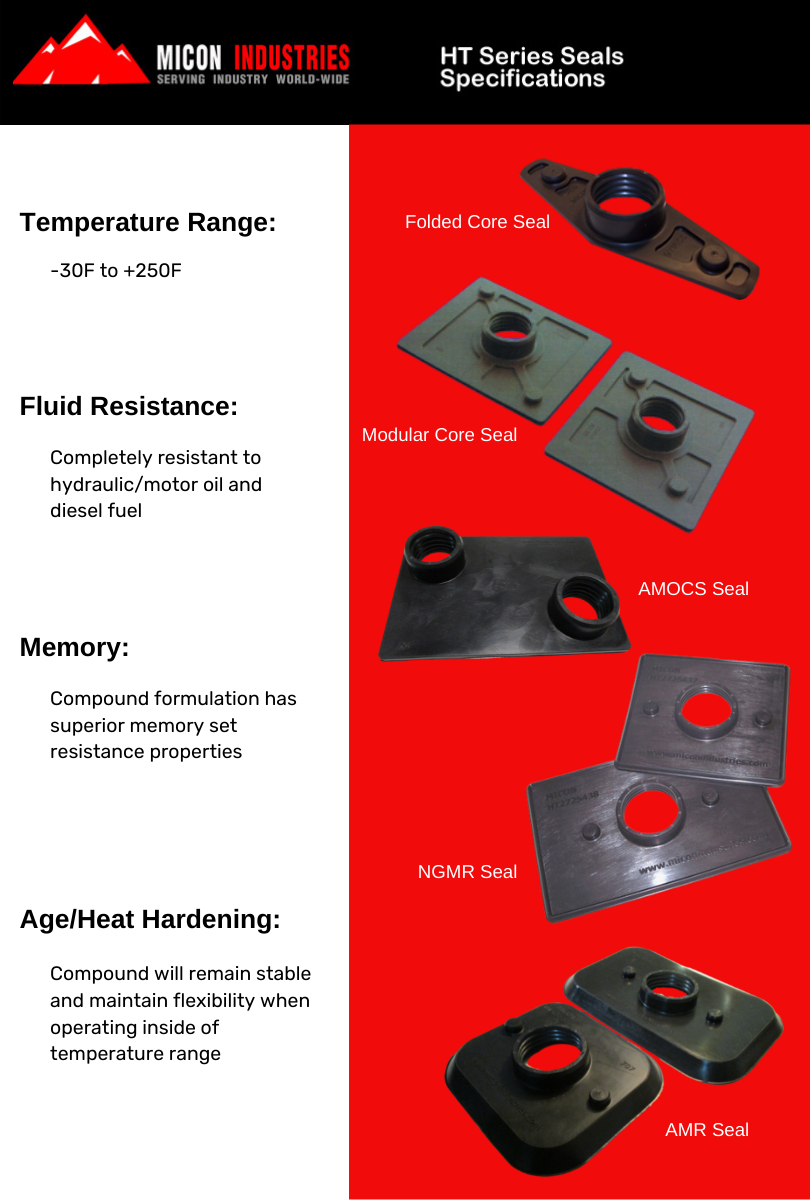
Micon Industries has spent years developing the HT Series Seals; the rubber formulation was developed specifically for radiators operating in all kinds of environments from everyday applications to the most extreme. The HT Series Seals are completely oil & fuel resistant and can operate at extremely high or low temperatures for years. The compound has incredible memory set resistance even after years of service in harsh environments. The HT Series Seals are regarded as the very best by cooling system professionals worldwide. Avoid failures and costly down time, use MICON HT Series Seals.
Next Generation Modular Radiator (NGMR) Seals
Micon now offers Next Generation Modular Radiator (NGMR) seals, the latest version of Caterpillar™ industrial radiator seals. Micon's NGMR seals have been formulated with their exclusive HT Series compound to ensure the seals offer the best heat & diesel / oil resistance in the industry.
Aluminum Modular Radiator (AMR) Seals
The AMR seal (Aluminum Modular Radiator) is the next seal in the next generation series seals, commonly used in applications where Aluminum radiators are in place, The aluminum radiators in these applications are shorter to allow for the expansion of the aluminum core, the seals have a thicker design to make up for the reduced height of the radiator. AMR seals are made from the same HT series formulation and produced in a higher duro to endure the weight and expansion of the aluminum radiators. These seals are available wherever Micon seals are sold and come with a two year warranty.
Common OEM Seal Failures
Heat Exhaustion
This can occur when the operating temperature range of the rubber has been exceeded. The effects on the seal can include reduction of seal flexibility and hardening, leading to leakage.
Oil/Diesel Contamination
This is a common problem in cooling systems. If an oil cooler bundle leaks or a cylinder liner cracks, radiator seals can be exposed to fuel/oil through the cooling system. If the seals are not rated for these fluids they can start to absorb them, then often swelling up and becoming soft and "spongy". Once this occurs the radiators will begin to leak.
Incorrect Installation
Care must be taken to align the radiator with the seals. If a seal is "pinched" during reassembly it can often cause leakage on initial testing or reduce the service life of the radiator.